Three Conditions to Monitor for Visual Color Evaluations
The evaluation of the color of a batch or sample can be different for every application. Many coloration applications, like textiles, paints, inks, and plastics, require visual assessments along with instrumental measurements. While instrumental data is important, visual data allows technicians to evaluate how the color will appear to the naked eye of consumers.
Visual assessments identify differences between a batch color and its standard. They also compare human visual perception with reflectance data. As a part of quality control, performing these assessments early in the coloration process helps to eliminate the need for reworks and additional costs later.
There are three conditions to follow in order to yield good visual assessment results. Paying attention to these conditions allows for accurate and consistent results. These include lighting, observer, and viewing conditions. Let’s discuss the best practices for getting the best results during these visual assessments.
1. Lighting Conditions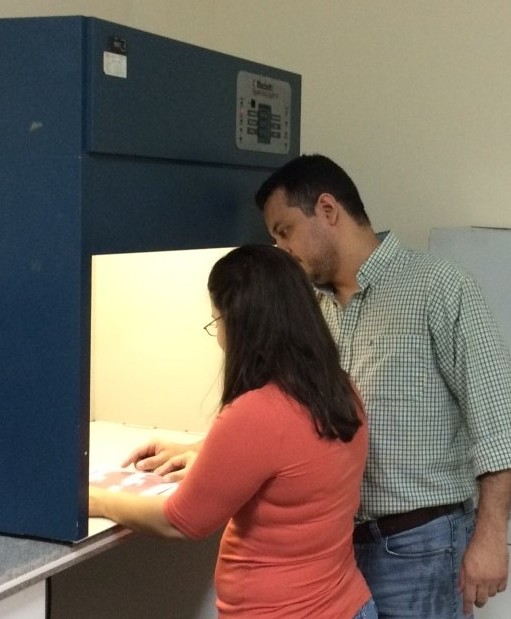
The shade of a color can alter under different light sources. The bright lights a customer may purchase a product from in a department store can impart a different shade in the product versus when they look at it in natural daylight. Lighting variables often lead to inconsistent batch colors as compared to the customer standard. To prevent inconsistencies, you should standardize the lighting conditions. When we process colors in our lab, we always check with our customer to make sure we’re manufacturing the color based on their favored lighting.
Using a light booth can help monitor consistent lighting conditions. Keeping the booth maintained and calibrated each year will provide optimal viewing results. You will want to use light source integrity in each test. This means if a customer’s color standard uses CWF deg-10 for visual assessment, you should use CWF deg-10 to test the batch color. Light booths should be placed in a dark room, with no outside lighting, so that the visual assessment is not compromised from other light sources.
2.Observer Conditions
Everyone’s vision is different; we perceive color in our own way. Colors can appear different from one person to another. Even the color clothing you’re wearing can affect how you see the colors around you. To guarantee these visual assessments are taken into account, set and follow standard observer conditions to ensure consistent results.
3. Viewing Conditions
The manner in which a color is viewed also affects the result. Viewing from a slightly different angle or position, a color can appear off shade, brighter, duller, darker, or over saturated. When testing, the angle at which the sample is viewed must be consistent for each visual assessment.
When evaluating a sample color in the light booth, the booth must be free and clear of any other foreign objects. These objects can distract the eye from a correct assessment. The sample color and the customer color standard should be laid flat or at a 45-degree angle in the light booth.
We advise to create different viewing positions between the sample color and the customer color standard, shifting top to bottom or left to right. These different viewing positions allow for a more thorough visual assessment. Make sure the sample color and the customer color standard are parallel and touching each other. Lay them side by side so color differences between the two are more noticeable.
Using Visual Color Evaluations
Of the three conditions for doing a visual assessment of color, no one condition is more important than the others. All three conditions are needed to ensure a complete and thorough evaluation in color matching. Each condition has its own factors that can cause color inconsistencies or false conclusions.
It is important to set your conditions based on customer specifications. Administering visual assessments for color helps identify inconsistencies, which can help avoid reworks later. As a result, color efficiency improves and off shade or off quality colors are reduced. This leaves you with more operational efficiency and a happy end consumer.