Use FSW Tech Support! Get the Most From Dyes & Chemicals
Providing technical support isn’t just an add-on we throw out to customers for marketing. We notice if our customers aren’t using our products in the best manner or formulation, then their end results suffer. Our staff has years of experience in similar industries as our customers and they are well-versed in operational efficiencies to support the products used in manufacturing.
From textile and fiber coatings, coloration through all classes of dyes and pigments, and support of the products in manufacturing – we are well-versed in operational efficiencies to support our products in manufacturing. These levels of technical support can provide added value to the raw material you may be sourcing from us.
It’s factors like technical support that:
- Can’t be taught. And,
- Can make or break a supplier’s product performance.
We share these three case studies as examples of industries that saw better results with our products because of the technical support they received from our labs and staff. We dare you to challenge us with your chemical and colorant needs next!
Case #1: Enhancing Pigment Dispersion Systems
A new client approached us to help them improve their pigment dispersion application process. They wanted to develop a more robust and stable pigment dispersion system, so we went to work. The first thing we did was visit their facility and evaluate their application process. We wanted to see their operations in action.
With our application knowledge in their industry, we created a mechanical plan of improvement based on our visit and conversations. This plan also involved in-depth discussions with their application machinery manufacturer. With this, we were able to guide them to equipment that instantly corrected 80% of the application issues they were facing, while reducing chemical and colorant waste by 10%.
After fixing equipment inefficiencies, we then looked at the chemical and colorant products they used in the past. These were creating multiple issues for them, including:
- Clogging of in line filters.
- Lackluster color appearance of final substrate.
- Excessive use of chemical and colorant product.
- Lack of technical performance from the chemical or colorant product.
We undertook a series of lab experimentation with their substrate to see where we could improve upon these factors. We also took into account their end product goals that they weren’t able to achieve due to these constraints.
As a result, we provided a specialized pigment dispersion that gave a vast improvement in color intensity. The new product eliminated any clogging of their in-line filtering process, resulting in production efficiency. Using a higher strength product that reduced excessive use of the colorant also saved them money on logistics. Technical performance of the end product improved through lightfastness to outdoor UV degradation and improvement to repetitive moisture exposure.
By working together, utilizing FSW products and technical support, we were able to develop a holistic solution that tackled the problem from both sides of the issue.
Case #2: In-hand Samples for the Paper Industry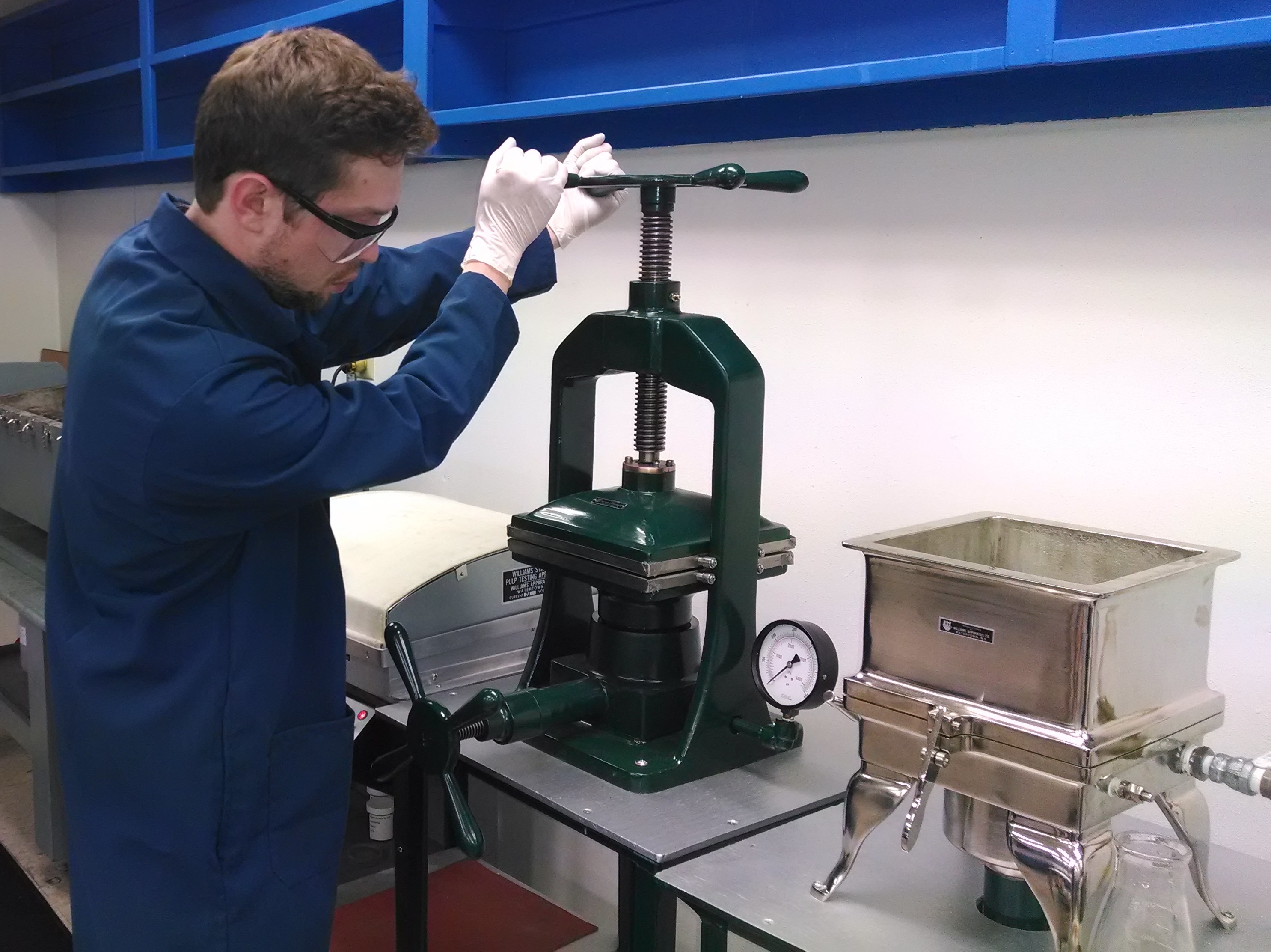
Several companies from the paper and pulp industry presented colorant opportunities to us more recently, and we knew we had to take action for this market. We invested in lab scale paper process equipment. This allowed us to provide physical color prototypes and matches to existing productions from our customers. We now have the ability to produce “hand sheets” in our laboratory pulp press!
With client-supplied raw material, we can take their pulp, process it, and add our colorant products and return a cured colored paper sample for their reviews. Whether using a dyestuff or pigmentation, we can work within the parameters of the customer’s material. Even additional chemical applications can be included in this process. Here again, the extended industry knowledge from our laboratory and technical sales staff allowed us to recognize the need and react to the paper market.
Case #3: R&D for Product Dispersion
Sometimes, client’s already have the product they need, but struggle to get it compatible within an environment. This additional R&D work is another area where we provide technical support.
A client needed help in taking existing chemistries and uniting them into a new all-in-one product. This compacted product would then have the ability to accept and perform with a nanoscale fiber material. The catch, the nanoscale fiber material wasn’t easily dispersed in a water based solution.
Through six months of stability, application, and full process studies we resulted in an innovative new product that proved successful in dispersing the nanoscale fiber material. Because of this, the client could diversify and enter a fresh market they had not previously been able to access.
Whether helping our clients work through application and process challenges, developing colorants and systems that provide performance and cost advantages, or innovating chemistry for the next market demand, First Source Worldwide helps our clients improve their product performance and bottom line. We’re willing to take the conversation beyond supply and price, to make sure you’re able to use our products to their best ability.