How to Make the Most of Your Leather Shaving Machine
There are no shortages of headaches that can plague your leather shaving department. These machines work hard. They need attention to avoid poor shaving and breakdown. For a real-time report of the machine’s performance, we can look at the leather as it comes out of the machine. As a shaving operator or supervisor, here are suggestions to help you with common challenges.
Blame the Tanner!
No kidding, you will be fighting a losing battle if the leather is too dry, too wet, too loose, too heavy, etc… The problem is the tanner is in the other room blaming the shavers as we speak!
So let’s put that aside and assume the tanner is making the most perfect piece of wet blue you have ever seen or touched (I haven’t met a tanner yet that didn’t).
Know Your Machine’s Capability
No matter how well it’s running, an older shaver cannot measure up to current models. New machines have more horsepower, better hydraulic systems, and heavier frames to support larger diameter rollers and cylinders. You will increase shave volume with better evenness. Know the limits of the machine and ensure it can maintain the production requirements you established.
If a new machine is not in the budget, the best option is to divide the workload in half and shave each side or hide twice. Tough pill to swallow, but the quality will be well worth the expense.
Looking to replace equipment? Read more on choosing between refurbished or new.
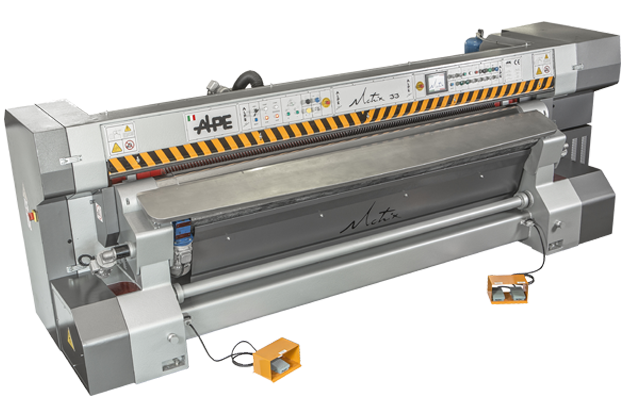
New shaving machine by Alpe, Italy
Reblading
Most chatter problems are the result of the blades. (Remember, the tanner has provided us the perfect leather.) Selecting a quality blade is critical – so know your supplier!
So, more importantly, installation!
Install blades using only copper tamping either by hand or an automatic reblading machine. Inspect and change bearings as needed with only top brand name bearings (or more often than needed – try every other set of blades as a rule, even if they seem fine). Once installed, rectify, level, and balance the blades on a high speed electronic balancing machine.
Use the Right Stone
This one is easy – Use only the stones recommended by the blade manufacturer for the type of blade you are using.
Most blades are made from hardened carbon steel. Some manufacturers offer various levels of blade hardness and bimetallic blades which provide a soft core and hardened shell. For each blade there is a recommended grinding stone grit, hardness, and bonding agent.
It is also important to respect the expiration date. The bonding agent deteriorates over time, making the stone brittle and prone to failure.
Sharpening and Grinding
When installing a fresh cylinder in the machine, the reblader should have already leveled it. Upon installation take as much time as needed to make sure the blades are leveled to the machine.
You’ll be looking for a spray of sparks from the stone as it travels across the working width of the machine. During the subsequent sharpening process, keep an eye on the sparks. If they are not staying even during sharpening, do not be afraid to revert back to the leveling operation a little longer. The level of spark coming from the stone should not exceed 12 inches during the normal operation of the machine.
Starting with a well-sharpened cylinder is critical — Now it’s a matter of grinding enough to keep the blades sharp as you run without overgrinding.
Keeping Blades Sharp – Avoid the Chatter Cycle
Establishing the cutting edge is a good start, but keeping it is another issue. Many things can cause chatter: a bad bearing, an unbalanced cylinder, an improperly installed blade, or too much moisture in the hide (I forget, that’s not a problem with our tanner!).
The problem is that the universal solution for chatter is to grind more. But overgrinding can lead to overheating and dulling of the blades…which results in more chatter. Once you lose the cutting edge of your blades, it is difficult to get it back. You’ll prematurely wear out your cylinder and continue to fight with intermittent chatter marks on your leather.
There is no easy fix here, but you can get assistance from the blade manufacturer and/or your reblader. This ongoing cycle of overgrinding can work against you, since the original cause of the chatter may go undiagnosed.
Don’t Forget Proper Maintenance
It goes without saying the rest of the machine must be in top running order. The grinding system, drive belts, bearings, bushings, and lubrication are top priority.
In theory, shaving is a simple process, without the need for skilled operators or complicated technology. Yet many tanneries continue to struggle with quality and thickness problems. Newer machinery can help, but these come at a premium price. No matter what machine you are working with, partnering with a reliable reblader and selecting the right blade can improve shaving. You’ll also see cost reduction by reducing blade and stone consumption; and, improving the quality of your leather.
Deciding between refurbished or new equipment? Download our checklist to guide your decision.